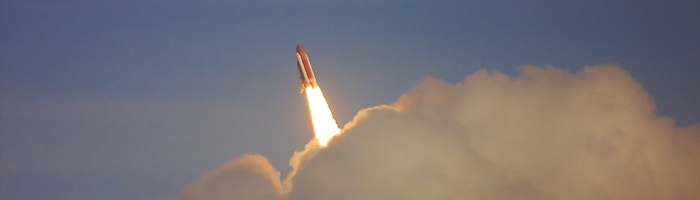
Mission-Critical: Sustainable Living and Working in Space
Did you know that it is now possible to successfully manufacture ceramic components in space via 3D printing technology? The Ceramic Manufacturing Model (CMM) was accomplished by Redwire in December 2020 making possible a world-first feat. It manufactured a single-piece ceramic turbine bladed disk or blisk.
Redwire is the leading developer of mission-critical solutions for next-generation space infrastructure, to deliver end-to-end solutions to meet the needs of customers and advance the future of space exploration.
Why ceramics?
The CMM can produce ceramics in space resulting in products of high-strength, excellent heat resistant properties, lower residual stresses and enhanced mechanical performance in comparison to components manufactured on Earth. Combustion engines, nuclear cores, and turbines can have even the most minimal improvement to strength for significantly greater longevity of the component’s lifespan.
Redwire will use additive stereolithography (SLA) technology to 3D print, as the CMM is the first SLA printer ever to operate in orbit. 3D printing ceramics in space could be conducted at full-scale, and industries on Earth could reap the benefits of accessing materials with enhanced properties. If successful, it will boost demand for components 3D printed in space, as awareness and understanding of the benefits grow across industries.
What will Redwire do next?
Redwire is to run a thorough analysis of the components back on Earth. The results will prove the superior quality of the space-manufactured components and further boost interest in space-produced products. More tests are needed to establish how large-scale production could occur and explore the range of components that can be manufactured in orbit. Space-manufactured parts may eventually become commonplace across industries in the coming years.