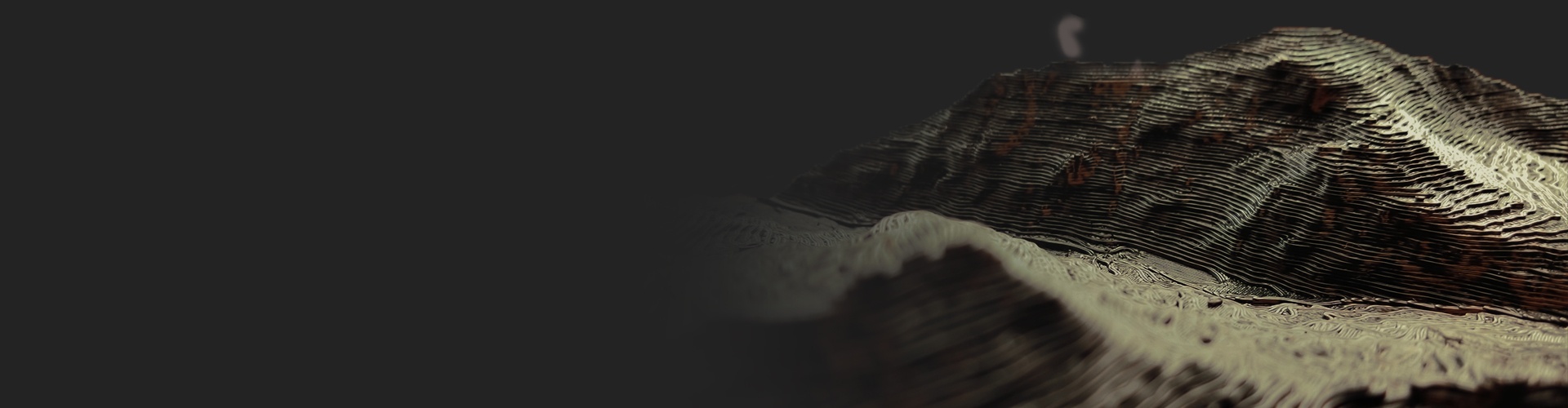
Fused Deposition Modeling
Leading the way / in 3D printing.
Printing, one layer at a time
The technology leader of 3D printing and industry manufacturing, fused deposition modelling (FDM) was patented by Stratasys in the early 1980’s.
Our family of professional line FDM printers utilize the technology by constructing three dimensional models from a heated supply of thermoplastic material and depositing it one layer at a time in a path dictated by the design program.
There are two materials that go into an FDM print job: the modeling material and the support material. The support material is used to hold up the structure during the build process. Both of these materials are fed through the print head and spread out across the x and y axis into a complete layer before the z axis moves up and begins the next layer. Once printing is complete, the support is broken away or dissolved in a bath, leaving only the final product.
Learn about our SAF process.
Build Envelope:
Up to 36” x 24” x 36” (914 x 609 x 914 mm). Oversized parts can be sectioned in the CAD file, 3D printed and reassembled in our bonding fixture using a structural adhesive.
Materials & Colors
FDM produces strong parts using production-grade thermoplastics. Each type of thermoplastic material has different properties that can enhance the quality of your part. Click on a material for more information.