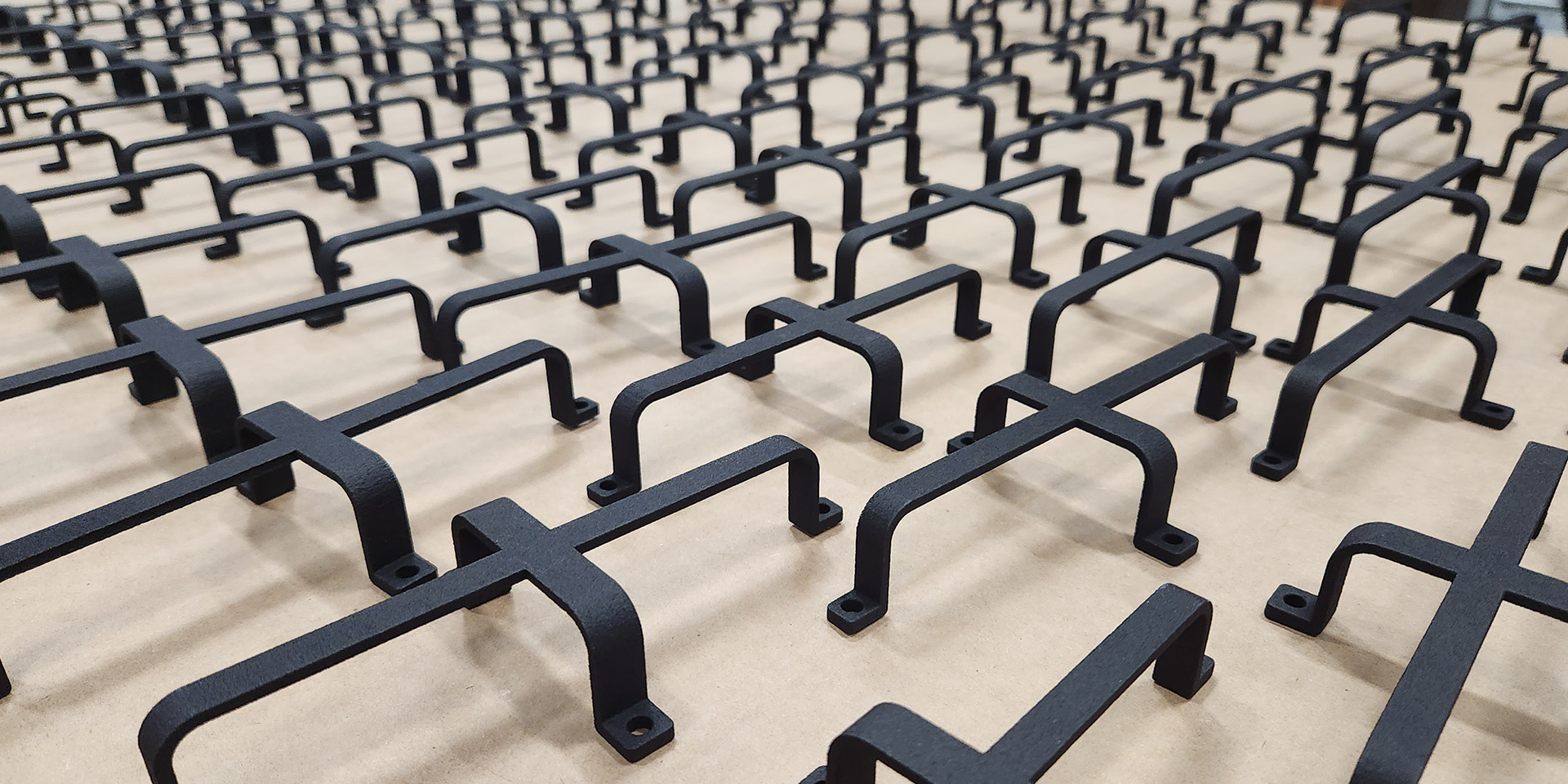
Injection molding and vacuum thermoforming are longstanding techniques used to manufacture parts with customized design elements. But they are expensive and creating individual tools for each design adds a significant amount of time to the manufacturing cycle. This month we worked with two companies to show how SAF™ (Selective Absorption Fusion) can truly bring those costs and times down.
The first was with a large automotive manufacturer. We received two designs that would typically be turned into two separate tools for injection molding. But since these were short production runs, yielding around 200 parts per design, we decided to 3D print with SAF. With that, we were able to forgo tooling and knock down the costs by about 50% per part.
Replacing injection molding with SAF™ 3D printing is proving to be a very beneficial solution. SAF can reduce lead times from weeks to a couple of days. It can produce more complex geometries and can more directly adjust for part variations without the need to create an entirely new tool. It also completely eliminates the post-production need for tooling maintenance and storage. Each of these features add to the cost saving aspects of SAF.
The second company, in the transportation and logistics industry, was one that we have worked with for the past couple of years. They had initially come to us with a prototype design that we 3D printed a tool for, and thermoformed the final parts in ABS. We successfully completed many production runs from the thermoforming tool, pulling thousands of parts. But this year when we were able to show them the strength of the PA12 nylon, they opted to update their design to be produced with SAF, eliminating tooling, and reducing their overall costs by 4 times.
If you are ready to start your injection molding and thermoforming projects, contact us to talk about your options and see how SAF can save you time and money on your next production cycle.