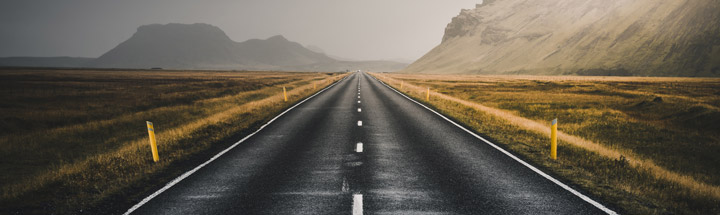
Even a Bugatti Can use 3D Printing
The “Divo” is the latest in a short line of modern supercars unraveled by the French luxury car maker, Bugatti. The reveal was made in an exclusive event in Monterey, California recently, the first of a limited production run of just 40 units. Matter-of-factly, all units were sold out in a matter of hours to the tune of $5.72 million each. The car featured some show-stopping features, part of its elegance were its rear grille and brake lights. They’re 3D-printed!
While beauty may be in the eye of the beholder, the partially 3D printed rear grill centerpiece added to the stunning aesthetics of the new Bugatti model. It’s an example of the car maker’s design philosophy – form follows performance – the engineers and designers aimed to create a vehicle focusing on cornering speeds and lateral dynamics.
The Divo claims to be not as fast as the Chiron, a previous production release, but makes its marks on the tracks nonetheless. It boast of superior cornering thanks to significant weight savings and an increase in downforce. It is the most agile car yet. It was developed to look different from the Chiron, but still recognizable as a Bugatti.
In the Divo’s rear, there’s a cascade of fins, 3D printed elements, forty-four pieces of which light up when the brake lights come on. It’s another step on an increasingly trodden path to additive manufacturing (AM) use in the automotive sector. Since the production for the car is small, only 40, 3D printing seems natural for the highly exclusive run. It is emphasizing design alongside the car’s performance.
Bugatti has used additive manufacturing before – on the Chiron supercar – with its 3D printing of a Titanium brake caliper. The piece was the largest and first 3D printed brake caliper, in addition to being the first use of Titanium in automotive production. The real value comes in the learnings it generates. With Bugatti serving as the Volkswagen Group’s R&D lab, it’s just a matter of time before results trickle down to everyday drives.
Partnering with Automotives in Seattle
Thinking of accessorizing your car, or seriously considering a parts replacement? Be that a prototype model or for a short run production, consider 3D Composites in Seattle. We’ve been partners with the industry for many trusting years.