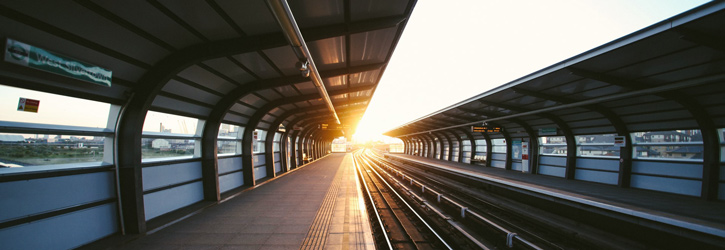
A Solution for Safety-Critical Parts
Deutsche Bahn AG or DB is a German railway company, jointly owned by the Federal Republic. It is the second-largest transport company in the world and is the largest railway operator and infrastructure owner in Europe. Their European system of high-speed trains is renowned for their comfort and reliability. With its annual carriage of about 2 billion passengers, from time to time the system requires repair.
Take for example, last year two rail carriages needed repair, requiring a new secondary roll stop, a heavy steel component bolted to the underside of each passenger car that limits lateral play on tight curves to ensure safe cornering. It’s a critical part for safety, though the engineers are hesitant to change it. The difficulty is that it is not a regular service item but an accident repair component that is not in stock normally. Needed urgently though, the usual suppliers said that the minimum order was for four castings, will take ten months to deliver, and still have them machined traditionally. On top of these, huge money is required for initial tooling. This just wouldn’t work. So they turned, instead, to 3D printing.
DB’s Head of Additive Manufacturing decided to 3D-print the components using the WAAM process, teaming up with Gefertec, which manufactured the parts at its headquarters near Berlin. The lead-time was reduced by five months and the overall cost was 30% lower. Gerfertec’s unique technology is that many kilograms of metal can be deposited in a relatively short time. DB’s secondary roll stops are perfect for the rapid production of high-value metal parts in small quantities at a reduced cost.
Before DB could realize the completed part there was a lot of investigation, development and design of processes with them at the outset, as this is a safety-critical component. Once the WAAM route was taken, the original 10-month lead-time for castings was down to half. In reality, during reconstruction the process can be condensed into a matter of days, and that despite having to work with Covid-19 restrictions.
This only goes to show that when it comes to a manufacturing process that involves a lengthy lead-time of hard-to-machine material – whether cast, forged or billet – an economical solution, such as Gerfertec’s, may be a viable commercial alternative to subtractive machining.