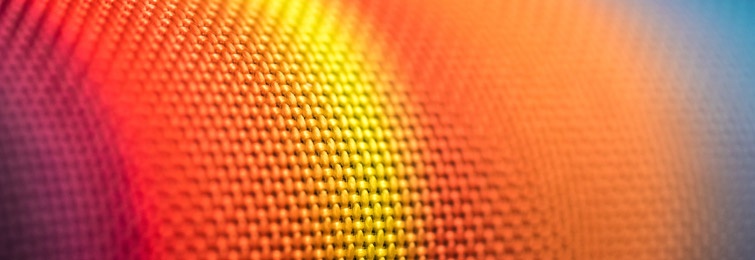
Looking For Next-Level Properties
3D printing enables us to see with the naked eye the physical properties of an object through changes in its microarchitecture. By 3D printing unique microgeometries, one can make a material behave in different ways. The architected materials used, also called metamaterials, have interesting applications across different industries.
Most desktop extrusion printers print architected materials. Users choose specific geometries with the infill setting in a print software to reduce the weight of the print, while maintaining structural integrity. The infill can be made denser with the choice of different patterns in order to modify the strength-to- weight ratio of the design. Yet, infill options for desktop printing are limited, the honeycomb shape being the most popular, and infill density can range from hollow to fully dense. However, the shape and the size of the shape can’t be modified throughout.
While the strength-to-weight ratio of an object is improved by architected materials, researchers have explored a number of different physical properties possible with architected materials.
Compression/cushioning
For example, the architected material used in helmet cushioning. By optimizing the microgeometry of a 3D-printed cushion, regions of a cushion can be made softer and more prone to compression and other regions stiffer.
4D Behavior
Some 3D-printed objects can be designed to behave differently when exposed to the environment. For example, an object that prints flat onto the print bed but folds automatically when removed and compressive forces are taken away. More complex examples are printing with materials that change when exposed to heat or water.
Soft Robotics
These are 3D-printed soft robots that move without using on-board electronics. They have a feature that, when exposed to the environment, causes them to behave in a certain way. For example, robots that, when compressed, cause limbs on a quadruped robot to twist and bend such that the robot moves forward.
Self-healing
Using a specialty developed photopolymer, they are printed objects that, when cut in half, could rejoin disparate parts upon exposure to 40 to 60°C (104 to 140°F) temperatures.
Shape-shifting
3D printing objects whose shapes can be modified after fabrication. These structures change shape through hand-manipulation. In others, pneumatic hoses are used to push air to soft, 3D-printed robots to drive their shape-shifting.