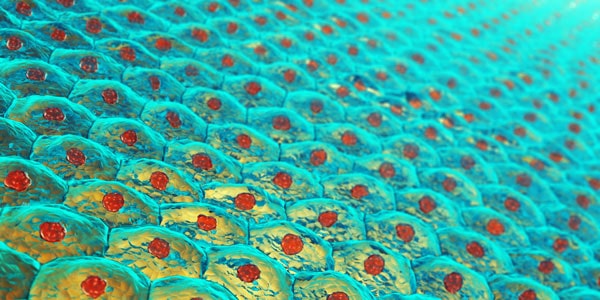
3D Printing Technology: Slowly But Surely
According to Paul Benning, Senior Fellow and Chief Technologist, 3D Printing, at HP Inc. (Palo Alto, CA), 3D printing technology, also known as additive manufacturing, has made significant, though incremental, strides in the last couple of years. He cites areas that remain challenges: material properties and seamless integration of 3D printing in the larger manufacturing environment.
The design process will get a boost from generative design. Generative design will automate the process by looking ahead at the design intent and suggests ways to fill in the design. Over time, engineers will be able to input the requirements of a part and a system that will spring up with lots of design variations until it evolves into the most lightweight and efficient design possible. Other production techniques cannot create designs and geometries like 3D printing can by using generative design.
Bioprinting
Bioprinting has made considerable advances in the past couple of years, but it is more than printed organs that can be transplanted into patients. Printing small, viable tissues, collections of cells that communicate with each other are the gists of bioprinting, not large organs. For example, testing a new drug with its basic small molecule interaction up to target molecules, then to cellular interactions. The richness of that environment gives R&D teams a much better system to study without having to do live animal studies.
We are not yet there in terms of livers and kidneys or other functional organs, but simpler tissues like cartilage and sections of bladder have been printed and transplanted into animals successfully. More relevant today are biocompatible materials for implantable applications, hearing aids, patient devices.
3D printing advances in functional color parts are becoming mainstream. It’s not only for aesthetics but, it also enables putting assembly instructions or wear indicators on a part, like UPC symbols or digital serial numbers on every single part. It helps track production from raw materials to end of life.
The industry has the core 3D-printing technologies – Multi Jet Fusion, selective laser sintering, stereo- lithography and binder jet additive manufacturing which will drive growth in bringing 3D-printed metal parts to the market. Likewise, the cost factors for 3D printing – runs of thousands to tens of thousands of parts – are economically advantageous, making 3D technology a much more productive and valuable part of the manufacturing ecosystem.
Getting There in Seattle This Year
Though considered a slow revolution, 3D printing is expected to make a more impact inroads in the manufacturing industry. We look forward to a more exciting and fruitful 2019.