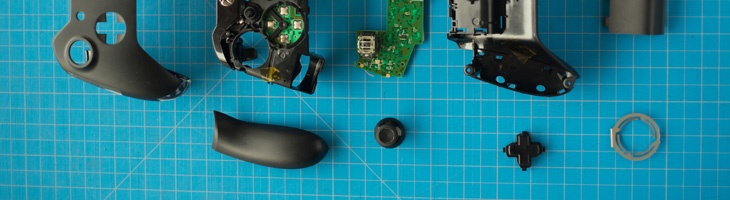
Winds of Change: From Traditional to 3D Printing
The spare parts manufacturing and logistics industry is worth a whopping $400 billion market. A couple of its biggest players are the aerospace and automotive sectors. We know that spare parts makers provide a steady stream of spare parts specific to each make and model for planes, trains, trucks, cars, etc. They are often complex parts produced in small series and sometimes for decades, in cases where equipment has a long life span, experiencing constant wear and tear.
As of late, the scenario is a’changing. 3D printing is looking like it is taking over the spare parts manufacturing and logistics industry. 3D printing is now making possible production of small-series parts, on demand and on location for major industries across the Us and the world. The technology can produce virtually any solid object, even those with complex architectures, and in a range of materials. Right now, about half of additive manufacturing is used for prototyping, saving manufacturers time and money, with less wastage and without expensive tools and molds.
Analysts and experts project that within three years fully 80% of global 3D printing capacity will be dedicated to making finished products. For example, General Electric expects to print 40,000 jet-fuel nozzles for aircraft by 2020. And that’s not good news for the traditional spare parts manufacturers.
Many major players are now investing heavily on 3d printing Research & Development. NASA and Boeing of aerospace are big investors. In the automotive manufacturing, Mercedes-Benz Trucks and BMW are players also, as well as Deutsche Bahn and Siemens in railways and transportation. These are just the early adapters but a wider sweep looks inevitable.
Logistics companies can ride this wave of change, to their own advantage actually, if they are willing to embrace the opportunity to develop market-leading B2B services. For example, turnkey spare parts management could be expanded to include spare parts on-demand solutions, like developing a virtual warehouse that securely stores CAD print files. Another option is putting up fabshops that offer localized print-on-demand and delivery services. They can also use their networks of distribution centers, warehouses, and sophisticated inventory management software. Most manufacturing and logistics organizations think they still have time to adapt to 3D printing shift, but this is becoming less true every passing year.
Open to Shifting Winds in Seattle
To all spare-parts manufacturers and logistics companies, for your working needs, come see us at 3D Composites. We have two convenient locations to serve you in Greater Seattle.