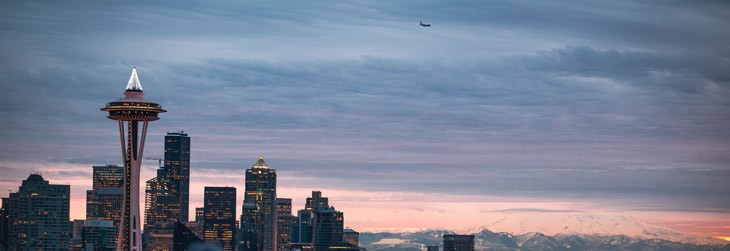
3D-Printing: Making Planes Lighter and Cheaper
Did you know that it’s customary for commercial jet programs to lose millions of dollars in the stage of research and engineering before they trim down expenses to make the manufacturing phase more efficient? This was so for Boeing Co., creator of the latest industry-leading technology called the 787 Dreamliner, touted for its unparalleled fuel efficiency and range flexibility.
The giant manufacturer have been losing money on each 787 made up until 2016, to the tune of $29 billion. Each Dreamliner uses titanium extensively. The alloy proves strong and lightweight, and keeps fuel efficiency better than aluminum, but costs seven times more. As of 2015, Boeing lost $30 million on the cost of each $265 million Dreamliner, with titanium parts accounting for $17 million of the overall price tag.
3D printing, the additive manufacturing technology trusted by aero engineers and designers for design, prototyping and manufacturing of parts, mechanisms and other flight structures, has been advancing the goals of airline and space manufacturers. Like others, Boeing is a big customer of 3D printing, previously deployed the technology in their jet engines and space taxis. This time, for their Dreamliner 787, titanium is the alloy of choice.
Norsk Titanium AS, the world’s pioneering supplier of additive-manufactured, structural titanium components today, with its patented Rapid Plasma Deposition™ (RPD™) process, has collaborated with Boeing Co. to provide their 3D-printed titanium structural components for the Dreamliner and other projects. It is added prestige for Norsk that their titanium components are first-time in the world approved by the Federal Aviation Authority. The approval was for structural, load-bearing components made out of titanium. This collaboration can spell a savings of almost $3million for Boeing per Dreamliner.
Taking to the Skies with 3D Printing in Seattle
3D printing has indeed advanced the way airline manufacturers make their planes and crafts. Pro 3D Composites has been serving the aerospace industry for many years, making possible safe and efficient flights over Seattle.