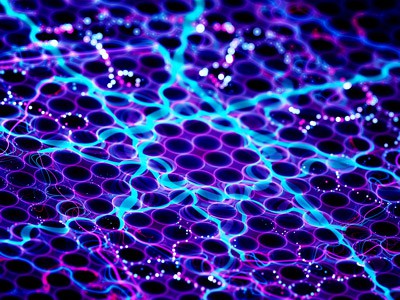
Breakthrough in 3D Printing Industry
We are all familiar with latex, that one which we find in paints and in gloves. The latex of the rubber tree is the main source of natural rubber. Actually, latex is a group of polymers coiled inside nanoparticles immersed in water. Latex and other like-rubbery materials called elastomers could be used for a variety of applications in 3D printing, including soft robotics, medical devices, or shock absorbers.
Researchers at Virginia Tech, one of the commonwealth’s most comprehensive universities and a leading research institution, have discovered a new process to 3D print latex rubber, showcasing the ability to print a variety of elastic materials with complex geometric shapes.
3D Printing Liquid Latex
The researchers chemically modified liquid latexes to make them printable and built a custom 3D printer with an embedded computer vision system to print accurate, high-resolution features of latex. They wanted latex in a solid 3D printed form, but liquid latex is extremely fragile and difficult for chemists to alter. So they built a scaffold around the latex particles to hold them in place and added photoinitiators and other compounds to the latex to 3D print with UV light. They used vat photopolymerization, in which the printer uses UV light to cure, or harden, a viscous resin into a specific shape. They built a new printer, which they patented, capable of printing high-resolution features across a large area.
However, the fluid latex particles caused scattering outside of the projected UV light which resulted in printing inaccurate parts. So they embedded a camera onto the printer to capture an image of each vat of latex resin. The machine is able to “see” the UV light’s interaction on the resin surface and then automatically adjust the printing parameters to correct the scattering to cure just the intended shape. They discovered their final 3D printed latex parts exhibited strong mechanical properties in a matrix known as a semi-interpenetrating polymer network, which hadn’t been documented for elastomeric latexes in the prior literature.
This research only shows that 3D printed latex provides the conceptual framework for printing a range of unprecedented materials from rigid plastics to soft rubbers, which have been unprintable until now. This just shows how pushing the boundary of what we assumed was the limit of a printed material’s performance came about through remarkable engineering.