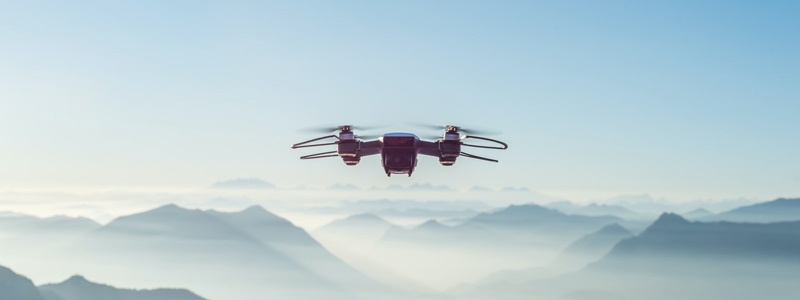
Drones and Satellites Benefit from 3D Printing
Satellite engineers at Airbus used 3D printing to create a titanium frame able to withstand temperature ranges of -170 to 100 degrees Celsius. Production costs were reduced by as much as 20%, creating a lighter and geometrically optimized product compared to previous iterations of the satellite. The startup Stratodyne utilizes rapid-prototyping methods with their filament to create bespoke stratospheric satellites that can be deployed in a few hours in close proximity to their targeted location.
The satellites can produce everything from asset monitoring to scientific measurements. These sustainable alternatives to satellites are even able to be used for telecommunications, remote sensing, or geospatial data collection. Unlike conventional satellites, which require months of testing, millions of dollars, and weeks to achieve orbit, StratoSats can be deployed in less than 24 hours for only a small cost. The company is currently developing near-space drones capable of extended duration flights as a cheap alternative to satellites.
3D Printed Rockets can take Humans to Mars
NASA and Virgin Orbit have begun testing a 3D printed rocket combustion chamber. Virgin Orbit uses its materials to air-launch rockets that generally carry small satellites into space. Virgin Orbit tapped NASA’s experts for the goal of creating a 3D printed combustion chamber, considered a rocket engine’s heart. Fuel and a source of oxygen called an oxidizer are mixed and exploded inside the chamber. The team was able to successfully test the combustion chamber using high-pressure liquid oxygen/kerosene propellants. The combustion chamber delivered more than 2,000 pounds of thrust successfully in nearly two-dozen, 60-second test firings. Normally, it takes many months to manufacture, test and deliver a conventional combustion chamber. 3D printing considerably reduced time.
3D Printing will make Trips to Deep Space More Manageable
According to NASA, to facilitate the living conditions of the astronauts on the International Space Station (ISS), which is only about 400 kilometers above the earth, annually the ISS needs to be provided with 3,175 kilos of spare parts, 13,154 kilos of spaceflight hardware spares, and another 17,690 kilos of spares ready to go at any time. But this is not practical or realistic on trips into the Moon and Mars. Even with enough supplies it would be extraordinarily costly and far from efficient. NASA In-Space Manufacturing (ISM) is currently investigating ways 3D printing technology could literally lighten the load of mission in space. They have developed fused filament fabrication 3D techniques, which involve feeding a continuous thread of plastic through a heated extruder and onto a tray layer by layer to create a three-dimensional object.
Currently, there is research exploring the most effectual methods of 3D printing in space, allowing astronauts to print simple tools, such as a wrench, or space food and other biological needs. Ultimately, ISM is critical for future exploration missions, and testing these manufacturing systems on the space station paves the way to enable those missions to be more independent of Earth.
Space agencies around the world look forward to all the potential ways 3D printing technology can be applied to the future of space travel. In the future, 3D printing could play a vital role in establishing long term colonies on Mars. By combining AI and robotics, additive manufacturing could play a crucial role in the creation of long term civilizations.