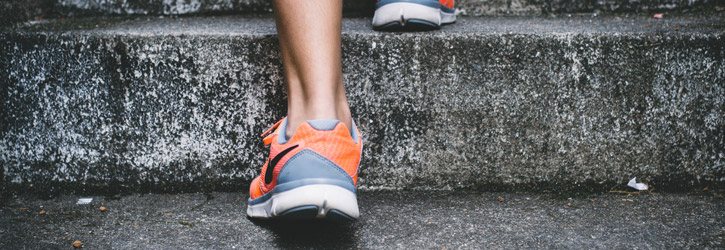
Value Proposition of 3D Printing
A team of undergraduate engineers of the University of Boston is choosing their senior capstone project finding interest in the field of printed footwear, specifically within the lack of literature in 3D midsoles in the context of running performance. Does using additive design in footwear provide both improved performance and value proposition?
3D Printed Midsole Design
While it is true that a simple piece of foam, so long as responsive, can make a difference in running performance, there are strides in development pushing the threshold by means of supplemental components. Foams now have embedded carbon-plates, airbags, and controversial tensile strands. There seems to be greater control over the midsole arrangement. The Boston engineers decide to examine ‘the enhancement of running performance through 3D printed midsole design’ as the foundation of their project.
The team printed 20 different lattice models and measured each for their percentage of energy return. Any shoe company minds the behavior of the midsole of the footwear in use which influences the return energy – the amount of energy retained as the structure, after being compressed, returns to its normal shape. This value, in turn, lowers the metabolic cost of running and pays significant dividends when cumulated over an entire marathon. They had help from a Formlabs SLA printer and elastic resin along with a license to nTopology’s previous software. The lattice structures benefited their study by providing three times the strength of foams at an equal density, and distributing the transferred energy more evenly within each step and at a slower rate. This offers greater stability and lower impact over time.
So here is seen the impact of additive manufacturing in transforming the overall design process. It benefits companies by cutting down waiting time for mock-ups to be built overseas only to have large batches of finished products deemed unacceptable and money wasted. Production can rapidly create prototypes on-site for instant feedback, streamlining the concept process. Time and cost of transporting parts and the length of supply chains are reduced. More importantly, additive manufacturing has the ability to construct complex parts at a lower cost than traditional processes.