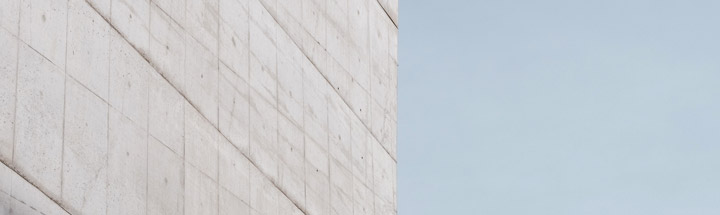
3D Printed Barracks: Fast and Safer Option
At the US Army Engineer Research and Development Center in Champaign, Illinois, you will find the largest barracks room ever built. It was constructed in early August this year, 2018 by the US Marines Corps, helped by the Army and Navy Seabees.
This development isn’t what is amazing about it, but that the 500-square foot barracks room was built using a specialized 3D concrete printer, the world’s largest, in just 40 hours. It is the world’s first continuous 3D-printed concrete barracks.
The Additive Manufacturing officer of the Marine Corps team said that the endeavor had never been done before. While buildings, homes and other large structures have been 3D-printed before, none have been done onsite and all at once. This is the first-in-the-world, onsite continuous concrete print.
The team used Computer Aided Design software on a 10-year-old computer. The concrete was pushed through a print head and layered repeatedly to build the barracks room walls. The Marines were carefully monitoring the project and continually filling the printer with concrete so the structure took 40 hours to build.If they had used a robot to do the mixing and pumping, the building could be built in 24 hours only.
There are several advantages of 3D-printed concrete. One is that it takes much less concrete to use compared to the traditional technique of filling a mold with concrete. The printer deposits only the concrete where it is needed, which decreases the use of cement. It is also a safer option as this reduces CO2 emissions, because cement production has a very high carbon footprint.
Where it takes ten Marines five days to construct a barracks hut out of wood, this technology saves time and additionally helps keep U.S. military personnel safe. In active or simulated combat environments, Marines are exposed unnecessarily in the open, plus fatigued out building the structure. Having a concrete printer that can make buildings on demand is a huge advantage. More testing will now be done on the Marines’ new barracks-building technology.
3D Printing Ideas Becoming Reality in Seattle
If there’s an idea brewing in your head and you just need to actualize it, drop by 3D Composites Seattle. Let’s talk possibilities and realities. Most things are possible with 3D printing.